In the market there is a considerable amount of competition as far as cutting machines are concerned, between the different cutting technologies, whether for sheet metal, tubes or profiles, or different cuts in metal.
There are those cutting machines that use mechanical abrasion cutting methods, but in this blog we will focus on thermal methods, such as plasma cutting and laser cutting, which will be better? Plasma cutting vs laser cutting?
Which of the two alternatives is the cheapest? What type of cut is the most accurate? What type of thickness are the various thermal cuts used for?
Next, we are going to explain the characteristics of each of the types of cuts and be able to choose the one that best suits our needs.
Plasma cutting
Plasma cutting emerged in the 1950s, due to the need to cut metals that could not be cut with a torch, for example, in the case of cutting materials such as stainless steel, aluminum and copper.
Plasma cutting is one of the fusion cutting processes, it is mainly used to cut conductive metals, such as brass, and as we have already mentioned, copper, aluminum or steel.
Plasma is one of the basic states of matter, the others being the solid, liquid, and gaseous states.
Plasma is a conductive gas that is heated to a high temperature. Gases consist of ionized molecules. Any group of positively charged particles and any group of negatively charged particles.
The heat generated in this process can reach temperatures of over 20,000 degrees Celsius, while the plasma flow from the nozzle can reach the speed of sound.
During cutting, the plasma is obtained by forced convection of a gas that is pressurized through a small diameter nozzle located inside the torch.
Normally, the gases used are oxygen, air, argon, hydrogen, nitrogen or a combination of them. The gas is then subjected to an electric arc that is located between the electrode and the piece to be cut.
The enormous thermal energy of the electric arc and the strong kinetic energy of the plasma gas allow the ejection of molten material and molten metal.
There are many variations of the plasma cutting process, designed to improve cut quality and arc stability, reduce noise and smoke, or increase cutting speed.
These differences depend on the amount of gas used, the amount of water used, etc. Plasma cutting can be combined with water jet cutting or anodized cutting.
The plasma cutting process uses electrically conductive gas, plasma gases include argon, hydrogen, nitrogen and mixtures, in addition to air and oxygen.
Plasma cutting can cut any type of metallic material, being especially suitable for steel. Plasma cutting allows for high definition and quality of cut.
Laser cut
In 1965 the first laser cutting machine was used, it was implemented to drill holes in diamond dies and until now it is one of the most used processes in the metalworking industry, laser cutting.
As its name indicates, the cutting is done by means of a beam of light, the laser provides great precision and speed when doing so.
Currently, laser cutting has many applications and can be used with many different materials, its applications range from cutting, welding, heat treatment, coating, vapor deposition, etc.
Not only in the metalworking industry is the laser cutter used, but it is also used in architecture, in the automobile industry for some accessories, and many more.
In short, it is a very versatile and flexible machine for many uses, since this type of machine offers the ability to work in very small areas due to the precision of the laser. You will be interested to see our blog: How does a laser cutter work?
In addition, because it can work on complicated surfaces, it allows the precision of the cut to be made exactly on the pieces that are intended to be cut.
Plasma cutting vs laser cutting
Laser cutting is a digital production technique, it is fast and far superior to other systems in terms of performance and productivity.
The plasma cutting process uses electrically conductive gas to transfer energy from an electrical power source through a plasma cutting torch.
Laser cutting makes clean cuts, as it does not leave many edges. For thicknesses greater than 20 mm, the quality of the laser cut is diminished.
Laser cutting allows you to cut very narrow, small pieces or make very small holes, thanks to its great precision. The quality of laser cutting is optimal in thicknesses measuring 15 to 20mm.
Plasma cutting allows a high definition and quality of cut, guaranteeing high-precision finishes.
Neither of these two types of cutting can perform 3D material cutting processes.
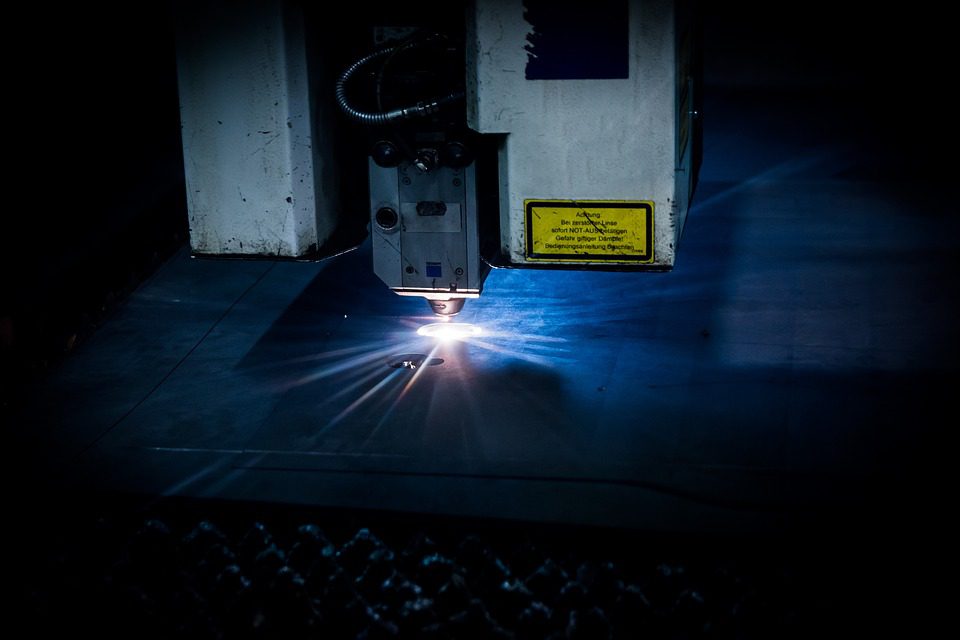
Another difference between laser cutting and plasma cutting is in the costs of the initial investment and operating costs.
Both costs to acquire a laser cutter are higher, since the cost of laser cutting equipment is very high compared to other material cutting technologies.
Laser cutting boasts an excellent finish.
Through plasma cutting all types of metal materials can be cut. Contrary to laser cutting, feet cannot cut excessively reflective metals because it depends on the thickness of the metal.
On the other hand, plasma cutting only cuts metallic materials and laser cutting can also be used to cut other non-metallic materials such as plastics, glass and wood.
The laser cutting It has many more applications than plasma cutting which is only used for cutting, however laser cutting can be used in cutting, drilling, engraving, ablation, structuring and welding processes.
In the market there are various processes of metal cutting, find the best variety of cutters in Perez Precision Works,, we are specialized in providing solutions in the metal cutting industry, since we have laser cutting and plasma cutting machines.